Carbon-dioxide-removal options are multiplying
Many are intriguing; none is cheap, scalable and easily verified
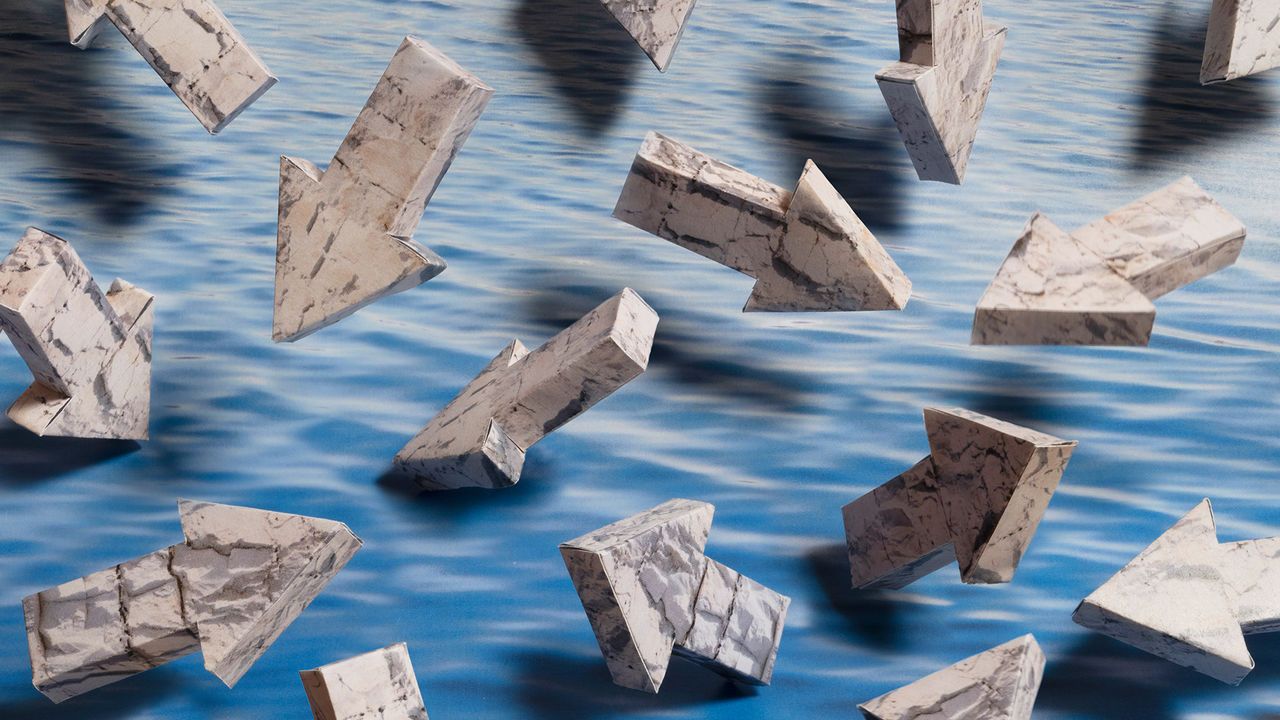
In what used to be a fish-processing plant in Akranes, a small port in Iceland, fragments of seaweed rise and fall in glass columns lit by leds. Running Tide, the Maine-based company which runs the facility, is trying to work out how best to get them to sporulate. The company needs spores in abundance to embed in the biodegradable buoys it is developing as a form of CDR. Once the buoys, made in part from biomass, are in the ocean, the spores will grow into deep-green fronds; after a certain amount of weed-growth and buoy-degradation, the whole kit and caboodle will become waterlogged and sink, transporting the carbon the seaweed has sucked up through photosynthesis to the bottom of the ocean.
In Brisbane, just south of San Francisco, an industrial building leased by Heirloom, another startup, has an oddly similar vibe: that of careful experiments aimed at optimising a pretty run-of-the-mill process about which no one has previously cared very much. Floor-to-ceiling racks like those you might see in a bakery are filled with trays of slaked lime, an alkaline compound made by first heating up limestone, a carbonate rock, so as to produce carbon dioxide and calcium oxide, or quicklime, and then reacting the quicklime with water. Expose this slaked lime to air and it absorbs carbon dioxide, turning back into limestone.
Heirloom is working on how to process that slaked lime and spread it on the trays so as to accelerate its regression to limestone. That limestone will then be fed into a type of oven called a calciner to be turned back into carbon dioxide (for storage) and quicklime that is ready to be slaked, trayed and fed through the whole process again. Sitting next to the calciner is a gas cylinder which contains the very first carbon dioxide to have been removed from the air this way. It is emblazoned with the proud signatures of most of the workforce.
There are scores of such companies currently scaling intriguing CDR ideas up into commercial propositions. Their number reflects a lot of idealism, interest from governments, venture capitalists and big tech, and the sheer number of ways in which cdr might be done. These myriad ways, though, are all prey to the CDR trilemma. An ideal CDR technique should store carbon in a way that is easily monitored and verified, so people can know how much carbon is stored; it should be able to work on a large scale; and its costs should be low. As is the way with trilemmas, achieving more than two out of three is hard.
In the scalable, verifiable but expensive camp sit the two companies which, in terms of investment, are the giants of the field, Climeworks and Carbon Engineering. These direct-air-capture (DAC) companies use banks of fans to pull air over a substance which sucks out the carbon dioxide (the firms each use a different substance). The amount of carbon dioxide such plants remove can be easily measured; just look at how much gas they are pumping into storage. Scalability seems to follow from the relatively small area involved. Facilities capable of a gigatonne a year would be very big, but city-sized, not country-sized.
But then there is price. In climate terms, today’s carbon-dioxide level of 417 parts per million is alarming; in chemical-engineering terms, removing something that represents just 0.04%, or one part in 2,400, of what you start with is hard. It means moving a lot of air and using a lot of energy. An overview published last year by Andrew Bergman and Anatoly Rinberg of Harvard University puts the energy needed to provide a gigatonne of pure carbon dioxide with dac at 1-1.3% of humankind’s total energy use in 2019.
Climeworks has in the past claimed that its system can remove carbon dioxide for $600 a tonne. Academic studies have suggested it may be a little higher. In 2018 the founder of Carbon Engineering, David Keith, and some colleagues published an academic paper arguing that, in principle, the cost of producing a tonne of pure carbon dioxide ready for geological storage using the company’s approach might be in the range of $90-230. But there is no indication that such costs have yet been achieved.
Why then is DAC so attractive that, in 2022, Climeworks drew in $650m of equity investment; that, in August 2023, Occidental Petroleum announced it was buying Carbon Engineering for $1.1bn; and that, in November, BlackRock, an investor, put $550m into Occidental’s development of a 500,000-tonne-a-year DAC plant outside Odessa, Texas? In the Carbon Engineering case a big part of the story is that pure carbon dioxide has a specific use in the oil industry. In some depleted oil reservoirs, pumping in carbon dioxide is the only way to get more oil out. Occidental has a lot of wells in the Permian basin that will not produce oil without “enhanced recovery” of this sort.
Giant sucking sounds
What is more, if it does it with carbon dioxide from its plant outside Odessa and can show that the gas stays buried after the oil comes out, then it will be paid handsomely for doing so. Section 45q of America’s tax code provides a tax credit for every tonne of carbon dioxide a company can show it has put into permanent storage. In 2022 the oddly named Inflation Reduction Act raised the 45q credit for carbon dioxide from dac to $180 a tonne.
America’s Department of Energy also has $3.5bn to spend on furthering CDR. It is using those funds to bring into being two new 1m-tonne-a-year DAC “hubs”, a Climeworks-centred one in Louisiana and an Occidental/Carbon Engineering-centred one in south Texas. Each is getting up to $600m. Heirloom will be participating in work at the Louisiana hub.
This support is quite modest compared, say, with the support received by solar power 20 years ago. It is huge compared with what is going into other forms of CDR. Yet the other forms still attract interest. Some think the challenge of separating carbon dioxide from the air will never allow dac to come in at $100 a tonne, the Department of Energy’s target.
One alternative approach is to take the carbon dioxide not from the air, but from water. When air sits over water, the amount of carbon dioxide dissolved in the water is in equilibrium with the amount in the air. If you put more carbon dioxide into the air some goes into the water, maintaining the equilibrium; if you take some out of the water, the level in the air goes down. Various companies are looking at ways of capturing carbon dioxide by processing a continuous flow of sea water chemically or electrically so as to extract its carbon dioxide; some see a synergy with desalination plants. As with DAC, though, a lot of energy will be required.
Another alternative is to let photosynthesis do the hard work of taking the carbon dioxide out of the air and then treat the biomass thus produced in a way that makes its carbon suitable for durable forms of storage. The best established approach to doing this is BECCS—bioenergy with carbon capture and storage. Grow a crop, get some energy out of it (most often by burning it) and then store the carbon dioxide given off in the process. This is already done in some American biofuel refineries; there are lots of plans for using it more broadly. Stockholm Exergi, which provides electricity and heating for most of Sweden’s capital city, has plans to capture 800,000 tonnes of carbon dioxide a year from its biomass-fired boilers.
The fact that BECCS provides energy as well as storing carbon has been seen as one of its charms. But to some it is a distraction. Even at a CDR price per tonne well below $100, the carbon content of biomass is worth much more than the energy to be gained from burning it. Store the carbon without building a power station and you lose some secondary revenue. But you also lose the considerable capital cost of building a power station and fitting its chimneys with carbon-capture technology.
Hence the interest in alternative ways of biomass with carbon removal and storage, or BiCRS (pronounced “bikers”, rather than “bickers”): find some biomass, treat it a way that prevents decomposition and dispose of it permanently. A London-based company called Brilliant Planet has operations in Morocco and Oman whose aim is pumping seawater into big ponds in coastal deserts, growing algae with it, drying the algae out and burying it. Charm Industrial, based in San Francisco, raised $100m this June for a system which turns biomass into a sort of carbon-rich oil and pumps it into geological storage. Graphyte, a startup which broke cover this November, plans to process biomass into dense bricks wrapped in a resistant polymer for burial. Backed by Breakthrough Energy Ventures, a fund set up by Bill Gates, it says it can operate at $100/tonne. It plans to start making bricks from timber- and rice-mill waste in Arkansas next year.
Woody waste also has a role in many schemes using biochar, an approach with a lot of supporters. As charcoal-makers have known since antiquity, if you burn wood without much oxygen you get a carbon-rich char. Plough this into the soil and it will often do the soil good while only slowly breaking down into a form bacteria and fungi can turn back into carbon dioxide. The carbon benefit is not just the carbon stored in the char, but also the carbon stored in the richer, healthier soil.
This has great appeal, but also two problems. Attempts to store more carbon in soil cannot be guaranteed to endure, especially since storage in soils, as in forests, will become less dependable as the world warms. The other is the durability of the biochar itself. Some particles of biochar stay charry for centuries; but how much of it will do so is not easy to say.
Spread it wide
Biochar does not provide the sort of durable storage a DAC system pumping carbon dioxide into an oil well or a borehole in basalt would. But other forms of BiCRS, such as those offered by Charm’s oil and Graphyte’s bricks, might well do. That would go a long way to making their removals verifiable, and thus marketable. But more is needed, because, as Bodie Cabiyo of Carbon Direct puts it, “All biomass has a counterfactual.”
Land growing biomass for BiCRS is not doing something else; and that something else would, itself, have done some, albeit temporary, carbon storage. Your carbon accounting has to consider that removal which didn’t happen as well as the removal which did. It is in part because of the difficulty of accounting for such counterfactuals that the methodologies used for forest-offsetting programmes run to hundreds of pages. How a scheme deals with these things can make a big difference to the amount of carbon it is certified as having removed.
Using waste products makes this accounting easier; there is no land-use change to consider. It should also help reduce the amount of land needed, which may be the biggest barrier between BiCRS and the big time. Raising crops so that their carbon content can be harvested and stored should be a considerably less land-intense form of CDR than growing trees. But if you are going to store away gigatonnes you will probably still need a great deal of land.
This leaves a third type of scheme: enhanced weathering. Take substances which react with carbon dioxide; spread them over the land or scatter them over the ocean; let nature’s chemistry take its course. On land you might use ground-up peridotites, like those found in the Arabian peninsula’s Hajar mountains, or basalt; in the ocean, limestone. When limestone dissolves the calcium ions released lead to bicarbonate ions being formed from the carbon dioxide already dissolved in the water, providing a removal.
Enhanced weathering means moving a lot of mass around. To get rid of 1Gt of carbon dioxide by scattering finely powdered limestone over the oceans you would need to load at least 2.3Gt of the stuff on board the ships doing the spreading. In 2020 David Beerling, of Sheffield University, and many co-authors looked at what the weathering of powdered basalt applied to croplands might achieve. They found that removing 1Gt of carbon dioxide a year would mean spreading 6Gt of basalt over roughly a quarter of the cropland in large farming nations.
But humans already move a lot of mass around; weigh up all the stuff extracted from the crust in a year and you get over 50Gt. Coal alone accounts for 8Gt. As those mines close, as close they must, could some of that effort be put towards upping limestone production (about 7Gt a year, mostly for cement)? If CDR is valued at $100 a tonne and one tonne of CDR requires 2.3 tonnes of limestone, the back of an envelope values a properly distributed tonne of limestone at $44. In 2021, the average price per tonne the coal industry was getting from power generators in America was $41.
The cost of crushing and distributing the rock would make things more complex and expensive. But the biggest problem with enhanced weathering may not be cost or scale, but verification. Empirical rules of thumb for how much CDR a certain sort of application to a certain sort of soil in a particular climate might be good enough to compare overall benefits with costs. Actually tracking the carbon stored thanks to a particular application of rock dust will not be possible.
That is bad news if you want to sell CDR credits. But farmers already spread many things on their fields, including, where soil is acidic, limestone. Especially if minerals weather in a way that enhances the soil, the carbon-removal benefit provided might be worth the cost of subsidising farmers to spread them. Some benefits really are best bought publicly. ■
This article appeared in the Special report section of the print edition under the headline "There must be 50 ways..."
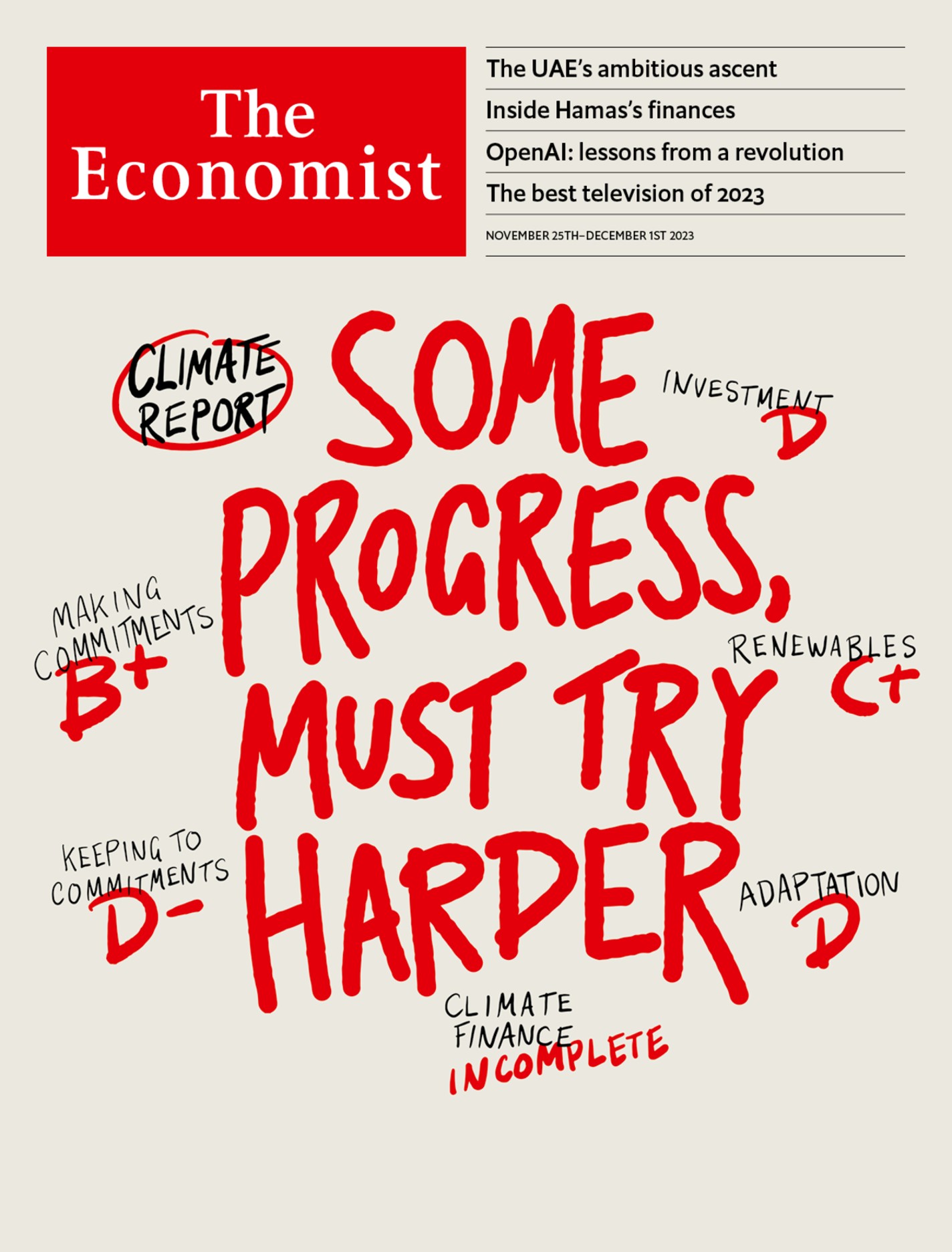
From the November 25th 2023 edition
Discover stories from this section and more in the list of contents
Explore the edition